With the increasing uncertainty and disruption in supply and demand, forecasting and planning can be challenging. We enable you to maintain optimum stock levels and respond quickly to fluctuations in customer demand and changes in the global supply chain.
ULTIMATE INVENTORY CONTROL TO SCALE YOUR BUSINESS, SUSTAINABLY
AGR turns the unpredictable into the predictable with powerful and easy to use inventory optimisation software.
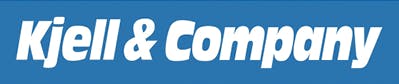

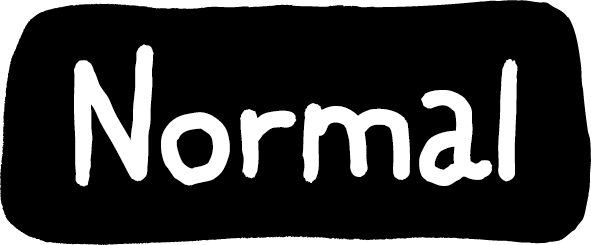
Optimise your supply chain in a fraction of the time
Our simple, intuitive inventory optimisation software provides you with the necessary tools to operate with precision and efficiency. Streamline your inventory, utilise best practice processes and incorporate the latest technology, such as AI, and turn your supply chain into a competitive advantage.
Make the unpredictable predictable
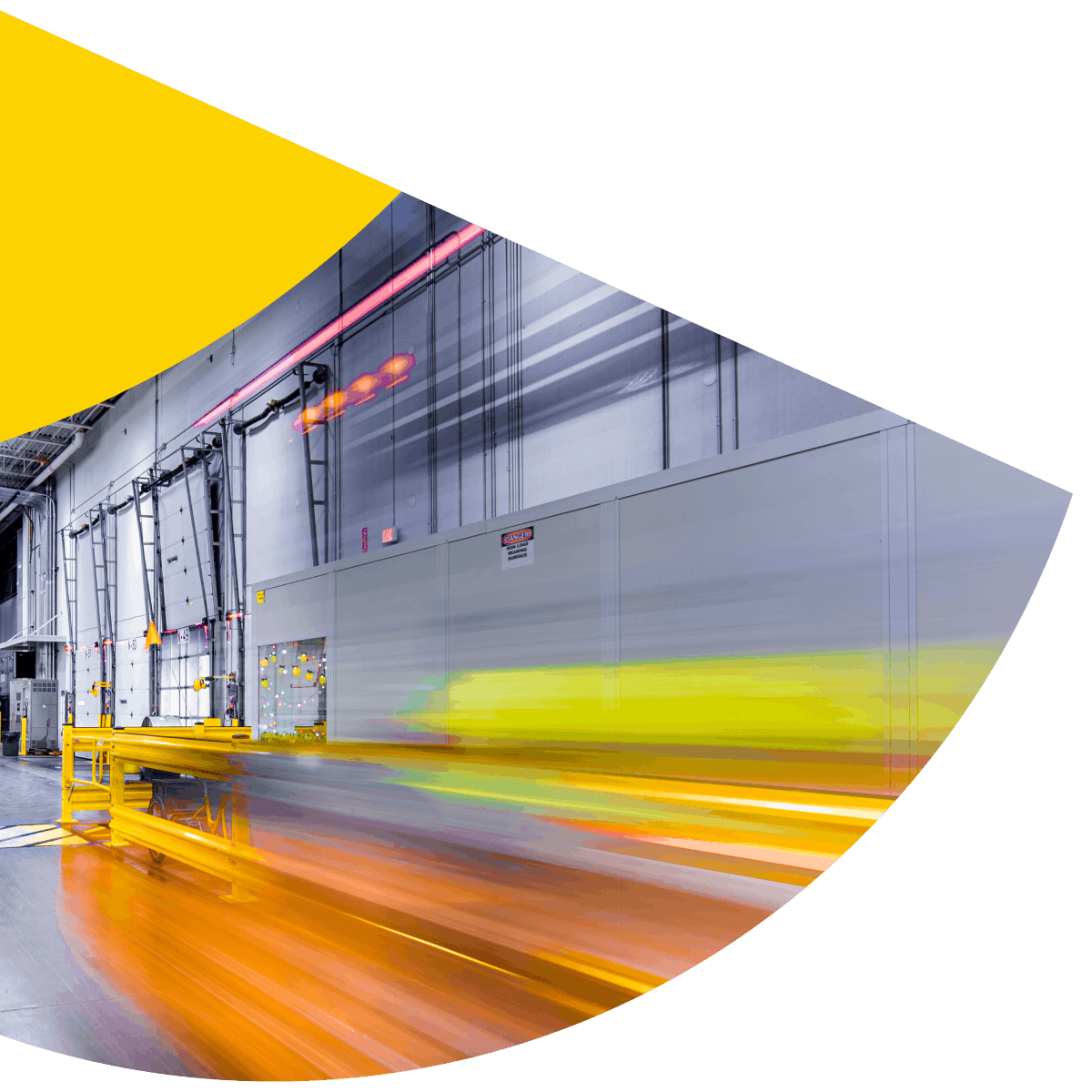
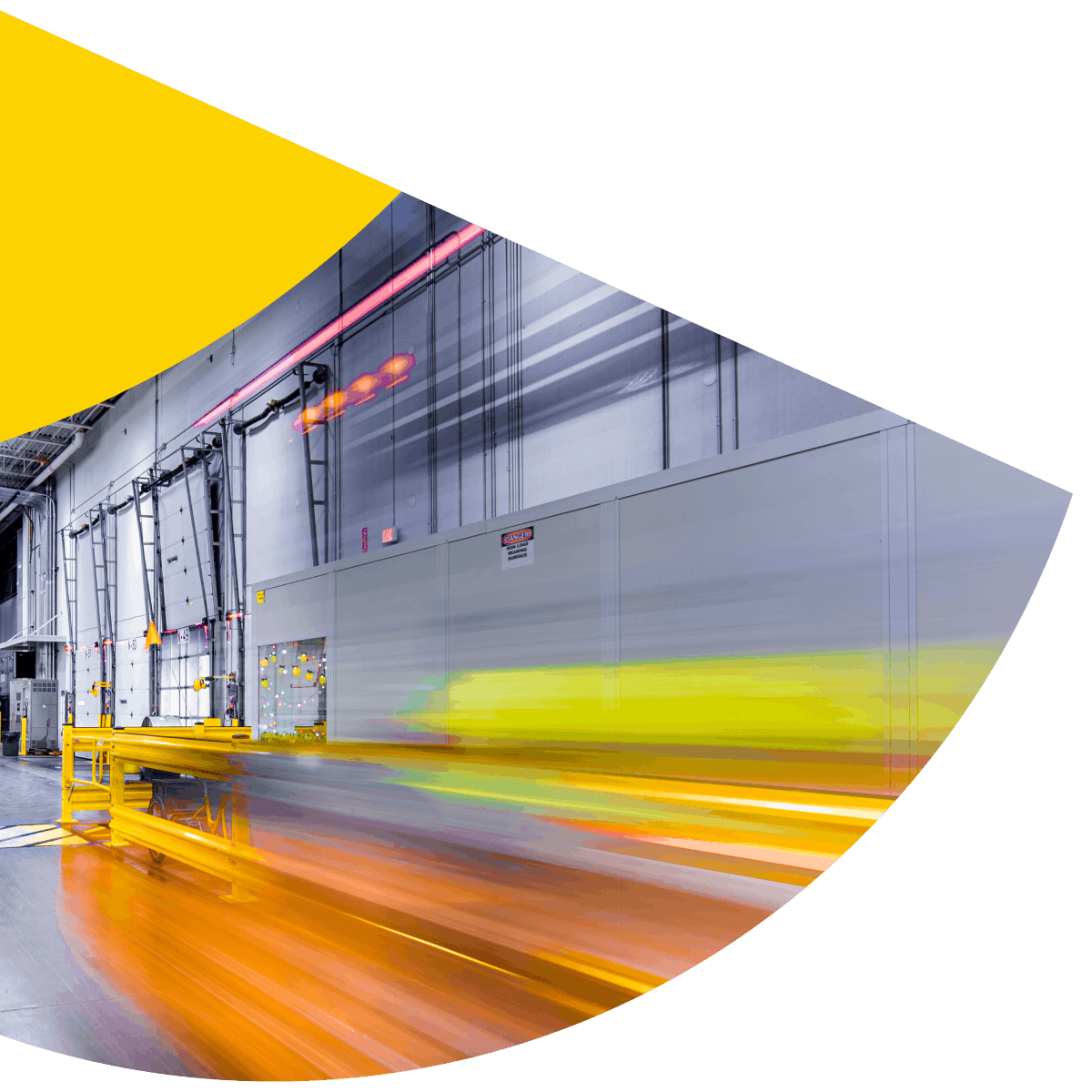
Minimise wasted resources
Companies and their supply chains play a critical role in building a sustainable economy and society. We are dedicated to helping businesses reduce mistaken investments, missed opportunities and wasted natural resources by improving the efficiency of the supply chain through inventory optimisation.
Boost productivity
Still relying on labour-intensive and time-consuming spreadsheets to do most of your forecasting and planning? Automate manual, repetitive and predictable tasks to free up time for more high-value work and improve your team’s efficiency and productivity.
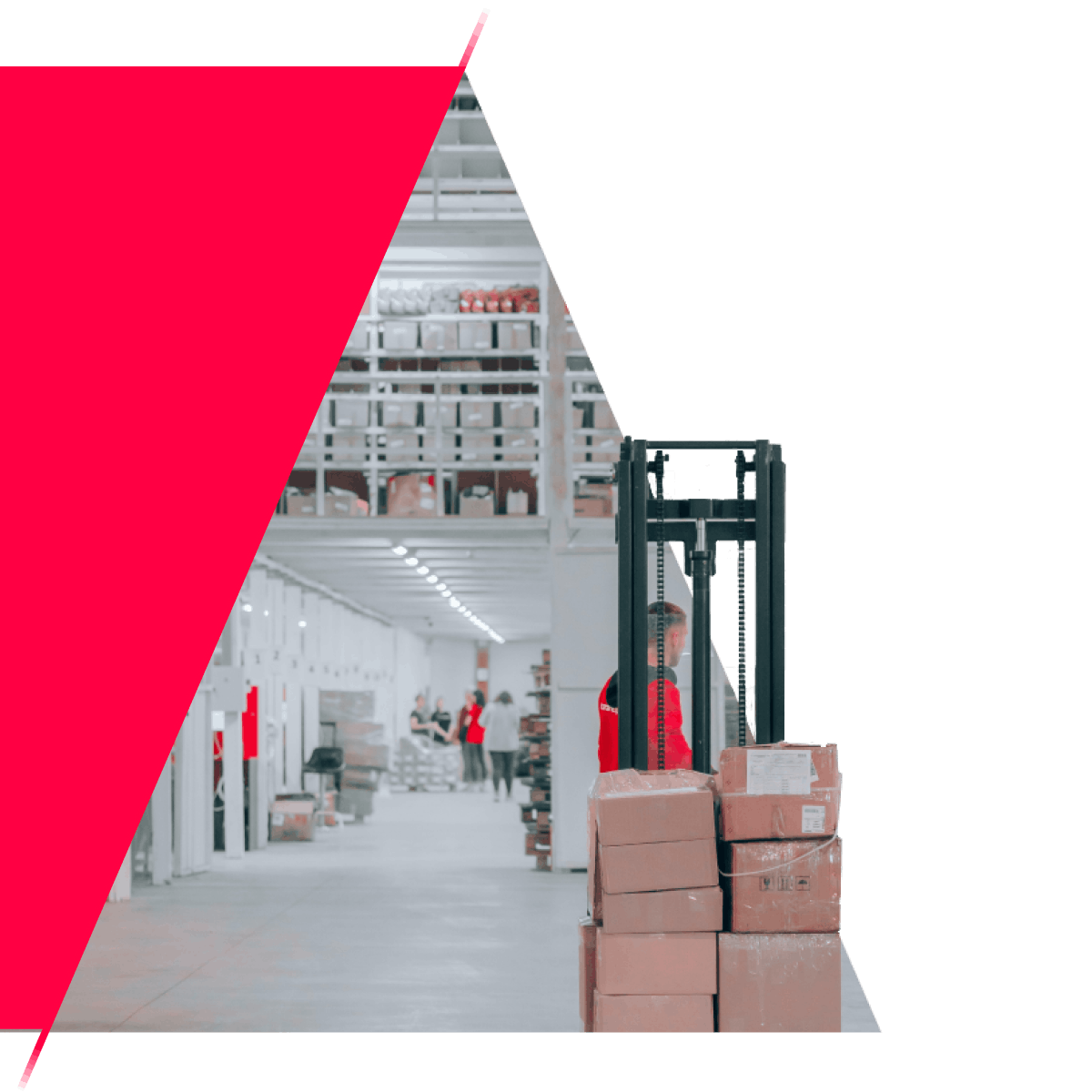
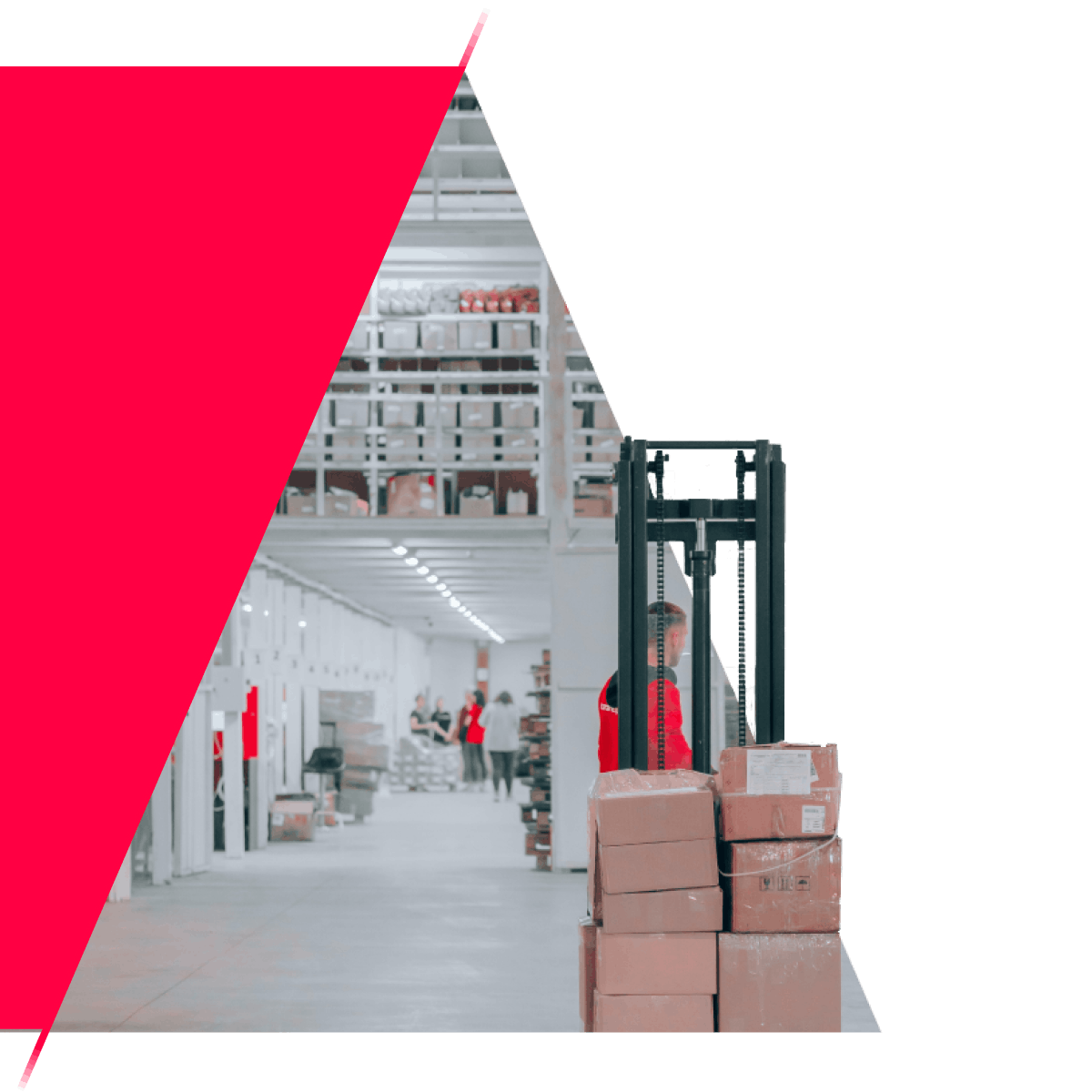
Gain visibility over stock levels
Gain an end-to-end view of your entire supply chain and start optimising your inventory from one fully ERP integrated, easy to use system with access to all the insights and reports you need to make the right decisions.
Drive internal alignment
Work from a single version of the truth. Enable more effective teamwork and remove silos by providing all relevant teams, such as inventory, sales, marketing and operations, with up-to-date and accurate inventory information.
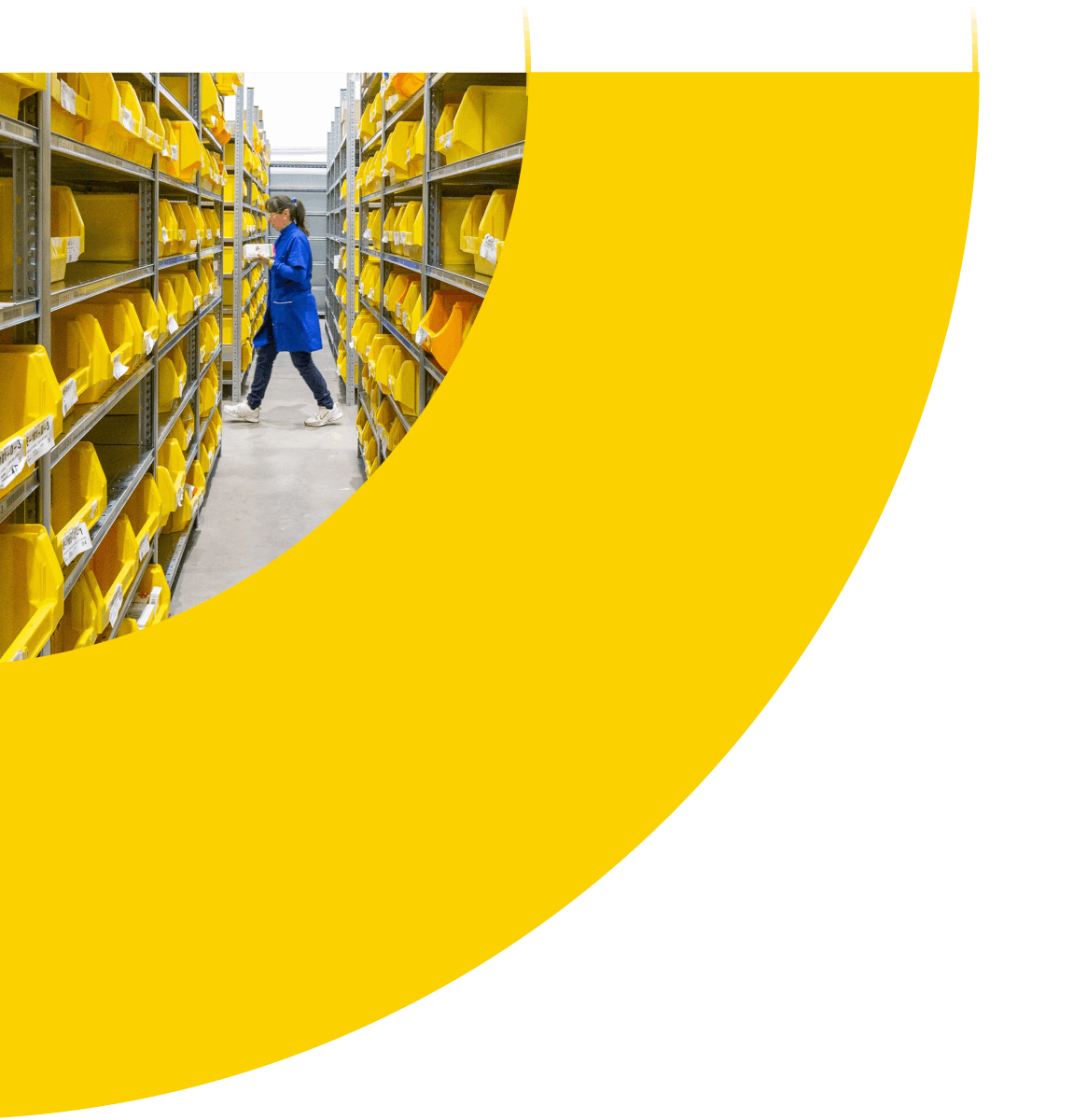
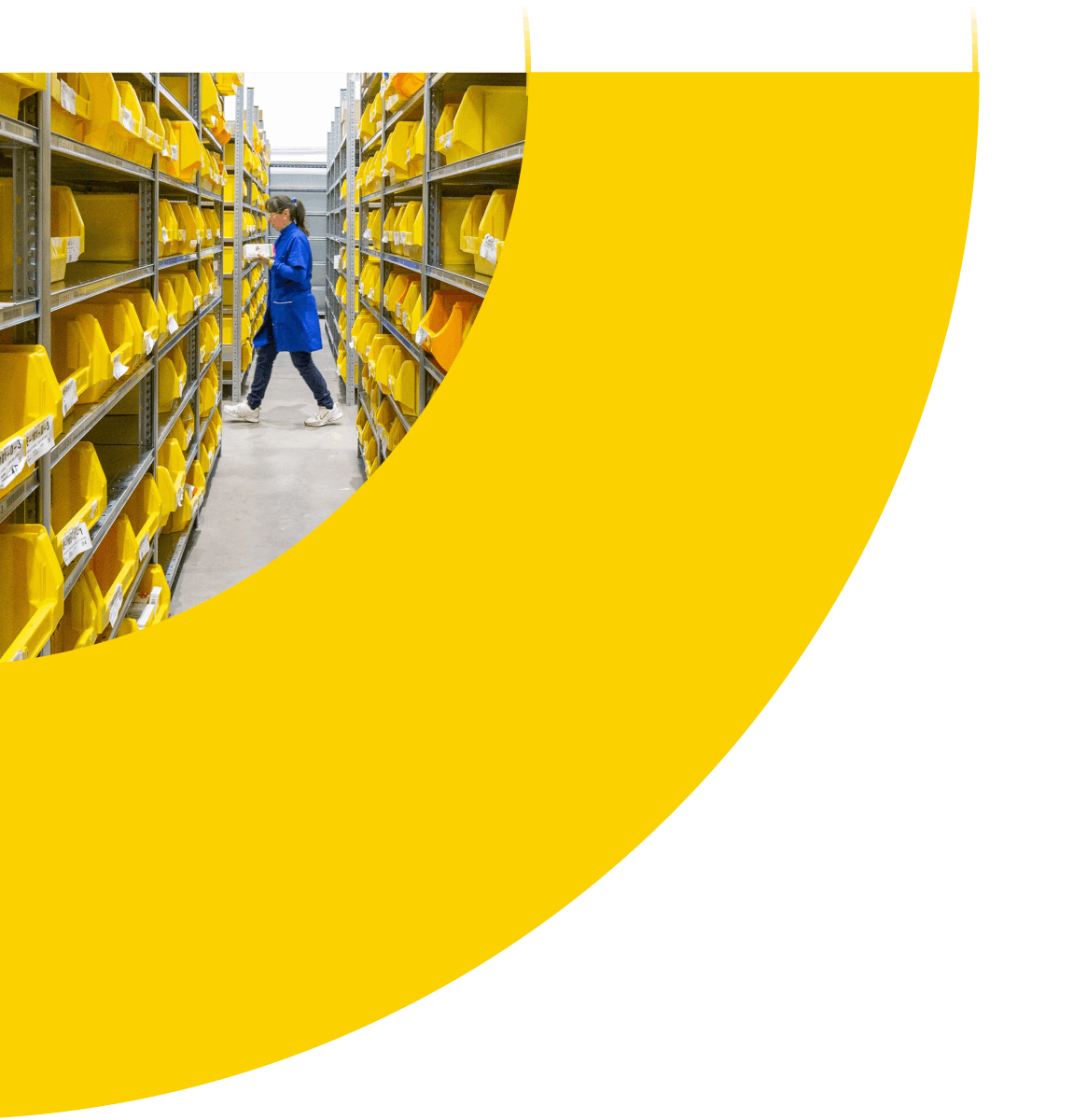
Unleash productivity with AGR Inventory Optimisation Software
AGR’s powerful Inventory Optimisation software provides you with Supply Chain visibility and control along with the transparency needed to respond to frequent changes and challenges in supply and demand.
Integrations
Unlock the power of your ERP with AGR
Free yourself from the limitations of your ERP and harness its data with AGR. Seamlessly connect to your ERP system and empower your team with the information and insights you need.
Why businesses choose AGR
Over the past 25 years we have worked in close co-operation with over 300 clients globally to transform their businesses. We are dedicated to eliminating waste in supply chains and will continue to perfect our toolset, allowing you to grow your business in times of uncertainty.
Hypercare
We strive to offer exceptional customer service at every turn. From the word go, you get assigned a dedicated support agent to guide you through the entire process. This is a longterm partnership and we are committed to helping you succeed and grow.
Simplicity
Intuitive, sophisticated yet simple user interface. AGR is designed to be as easy to use and transparent as possible, so your team won't want to be without it.
Sustainability
Enabling businesses to scale sustainably by providing the tools that drive effective inventory management and efficiency in resource, opportunity, time, and carbon.
Flexibility
AGR can be tailored to your business processes and supply chain to ensure a perfect fit. Choose from several configured workspaces and modules.
Why AGR is a market leader
0%
Reduction in inventory so you can operate profitably
<0
Months to achieve return on investment when you use AGR
0%
Reduction in manual tasks when using AGR
Boosting availability for Space NK, without increasing inventory investment
Renowned British beauty retailer, Space NK, offers the very best in beauty and runs 72 stores across the UK and Ireland, a further 29 in the US, as well as a thriving e-commerce platform. They implemented AGR in 2008 with the goal of improving their availability figures without having to invest in more inventory. Within a year of working with AGR they achieved their goal, as their availability went from 86% to 98% while their inventory reduced by 2-3%. Discover what they have to say about the AGR system.
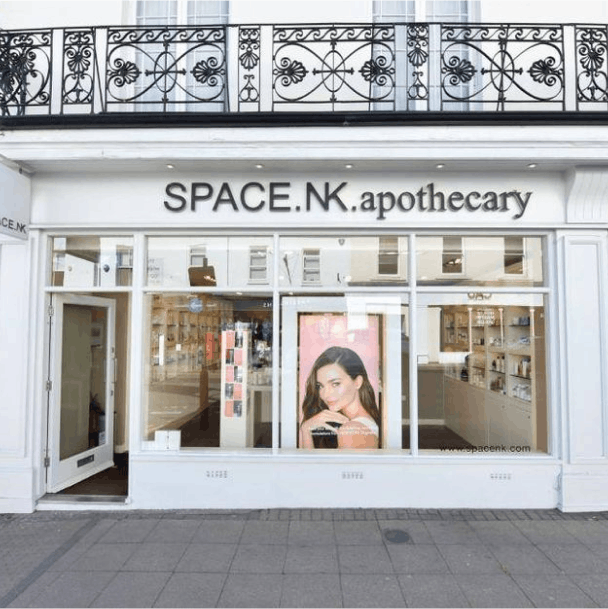
BoConcept
Today, leading Danish design brand BoConcept, launched in 1952, has close to two hundred stores in over fifty countries. The brand designs, produces and sells contemporary furniture, accessories and lighting for living, dining, sleeping, home-office and outdoor spaces. BoConcept went live with AGR in October 2018 and since they have gained a much better overview over their global operation as well as significantly reduced inventory levels.
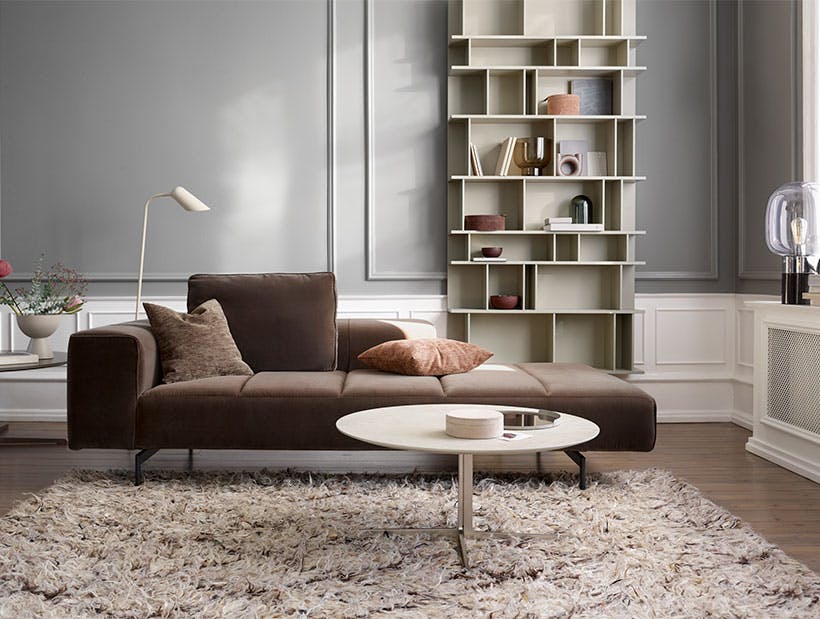
Søstrene Grene
Popular Danish retail chain Søstrene Grene, founded in 1973, provides a wide range of home and lifestyle products designed with Nordic inspiration and has over 250 stores all over Europe. They have been using AGR for their entire operation since 2019 and it has helped them achieve a better balance between inventory and service level as well as calculate accurate allocation based on store’s actual needs and sales.
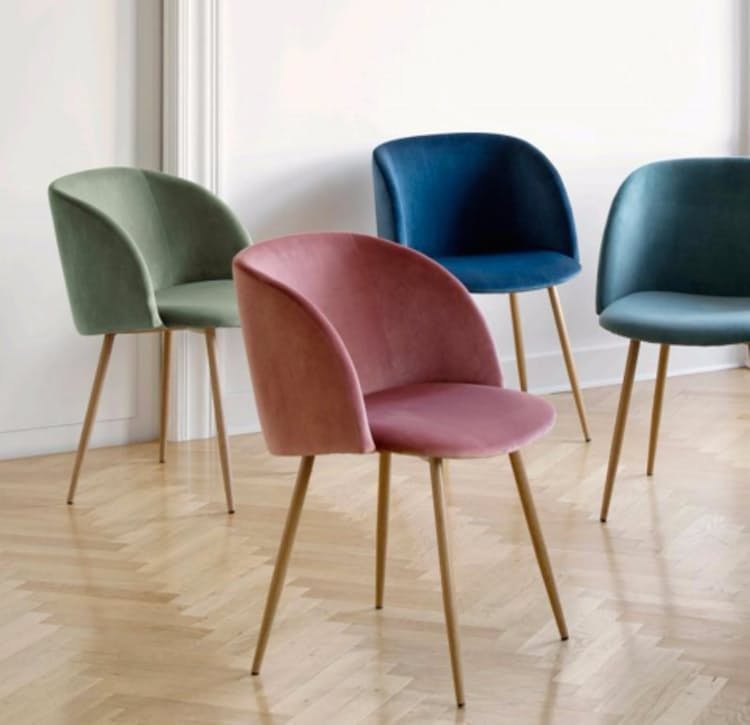
Rosendahl
Rosendahl Copenhagen was founded in 1984 and provides elegant yet functional Danish design for kitchen and home basics, made to last a lifetime. Rosendahl products are sold worldwide. Since implementing AGR they have benefitted from the accurate forecasts that have enabled them to reach an optimal balance between service level and inventory.
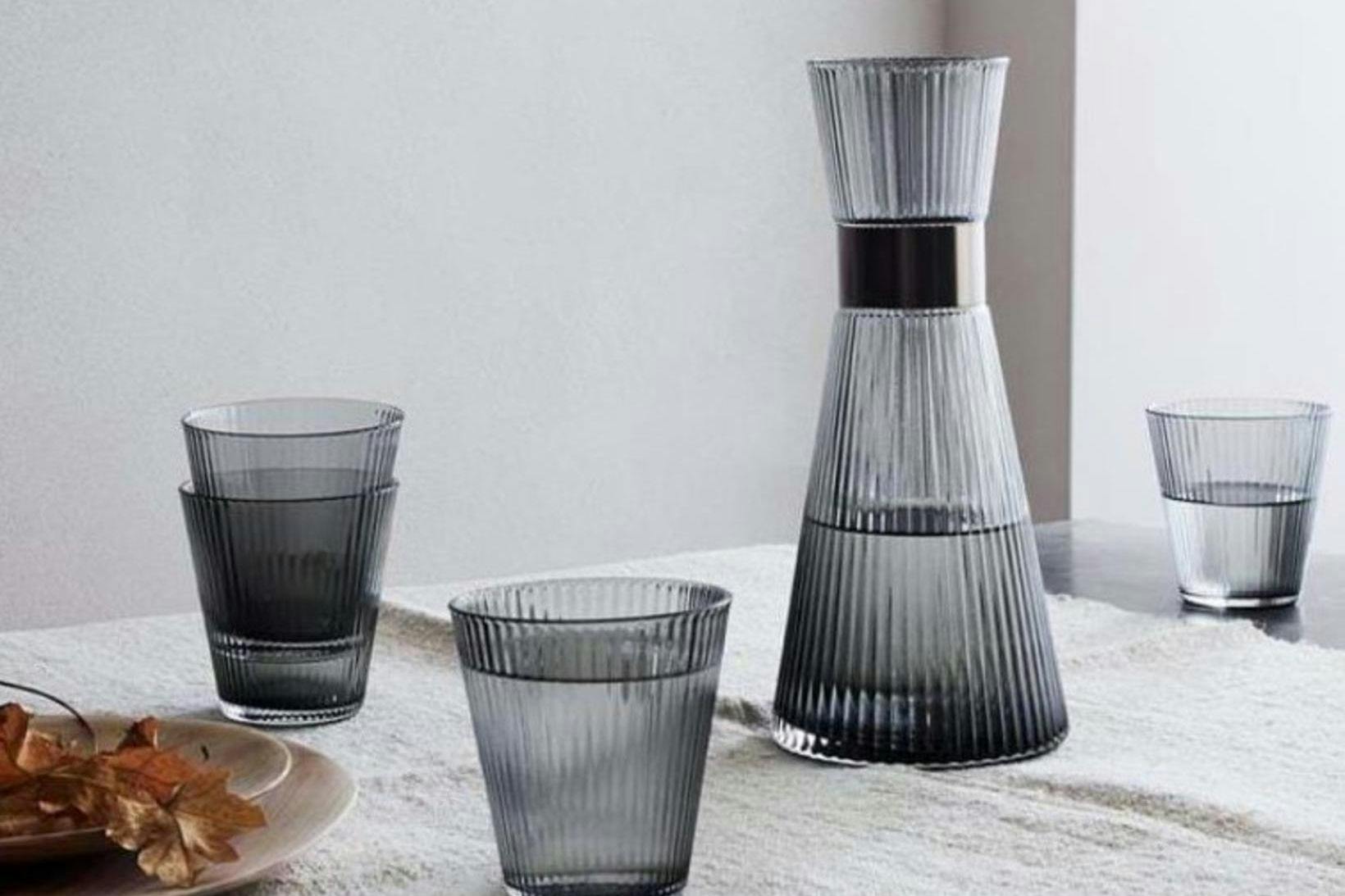
Get started with AGR
Discover our powerful inventory optimisation software and take control of your supply chain today.